At the request of @AdamG, I'm starting a thread on shipping fragile audio gear. I've gone through a whole slew of upgrades and audio trials over the last 5 years, to try new audio gear and in the process, I have learned a lot about shipping and receiving stuff. I've spent time shipping astronomy/astrophotography gear as well, which can be even more fragile and irreplaceable than any sort of audio gear and moved stuff into storage boxes.
I have been happy with USPS, UPS, and FedEx and have had my horror stories from all three. There can be a lot of variability with the delivery person assigned to your home, the use of temporary workers during the Holiday season, and simply bad luck. The thing to remember is that there are HUGE amounts of boxes going through the system and that translates into a lot of automated sorting. I don't work for any of the shipping companies, and I don't do commercial shipping, so if I have made a mistake, please let me know. I think I've done a lot of home-brew shipping of stuff without factory packaging.
My claim to fame is buying a Linn LP12 with no original packaging, no dust cover, or stylus cover featuring an irreplaceable Monster Cable Sigma 2000 moving coil cartridge from an estate sale where the selling party had minimal knowledge of audio gear but a willingness to take the packaging steps necessary to ensure its safe arrival (since I offered to pay a "handling fee" to go with the shipping). The most impressive packaging job I've seen was buying a JBL S/2600 "Baby Everest" from Japan. These are 125lb floor standing speakers. This was dedicated freight where a box truck was needed to deliver the speakers. When the driver opened the rear gate, he was mortified to see that the strap holding the speaker upright to the side of the vehicle had failed and the speaker had fallen off the wood pallet and keeled over to its side at some point during transit -- and there was zero damage.
Q. I have an original, never before released, master copy of a Beatles recording they made. There is one in the world, it's priceless, and I need to ship it with maximum insurance.
A. You want USPS registered mail
FedEx puts out a nice document on best practices with a lot of nice detail and photos. UPS has a guide also, but has fewer photos.
Step 1: Know your tape adhesive
If you have had to move a large apartment or home, you've likely had to deal with a lot of moving boxes. While it can be tempting to get the cheapest tape you can find off Amazon, you'll often find that generic ones falls apart or they'll have a noxious odor. Choosing the right tape is actually essential when shipping heavy audio gear. The best packaging doesn't help if your tape fails you. For convenience, I will refer to 3M consumer tapes since they're readily available and my preferred choice. There's a whole world of industrial tapes too.
You basically have two options for adhesives: Acrylic and Hot Melt Adhesives.
Acrylic adhesives are often used in "storage tape"
These types of adhesives are an emulsion which allows to deal with dusty boxes and are also UV resistant and water-resistant. So, it's theoretically a good choice if you're shipping during rainy season or sending stuff somewhere humid. But you know what acrylic tape is bad for? Strength.
Hot melt adhesives are probably what you want when shipping electronics. These use a synthetic rubber/resin adhesive which isn't as UV resistant, temperature or water resistant as the acrylic emulsion adhesive but they are stickier and won't accidentally release. Hot melt adhesives are what you want for rough handling of boxes, such as with automated processes.
What's the difference between the various hot melt adhesive products from Scotch? No real idea, but there are subtle differences in the advertised performance.
TLDR? Heavy Duty is probably better for heavier objects because it has the official 80 lb rating but is only rated to as low as 40 degrees F. The Box Lock has really high adhesion, even against the industrial tapes, but breaks at 150% elongation as compared to 160% suggesting that it might not hold heavier objects. The Box Lock has a wider range of operating temperatures including sub-freezing temperatures.
Step 2: Know your boxes
There are companies that are known for shipping fragile items safely. McIntosh is one. If you're dealing with well-established brands with good perceived customer service, step 1 is to reach out to the company for boxes. Without naming names, I've gotten huge speaker boxes and packaging material for free from an audiophile speaker company just for asking and purchased dedicated boxes with the product specific foam inserts from other companies at very reasonable prices. If you're dealing with something expensive and fragile, reach out to the company to see if you can buy a replacement shipping box first. In most cases, the shipping box and product box are the same -- but that is not always true.
People know about single- and double- wall board, but even for double walled cardboard, there are different types of corrugation/flutes and even different standards for box ratings.
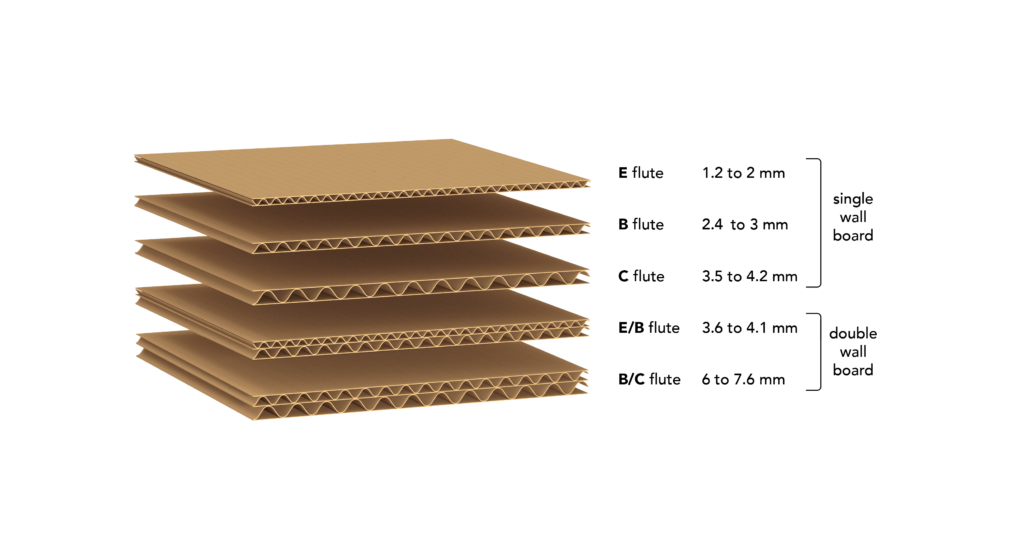
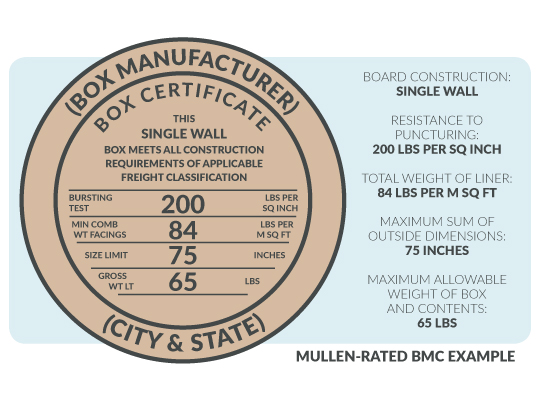
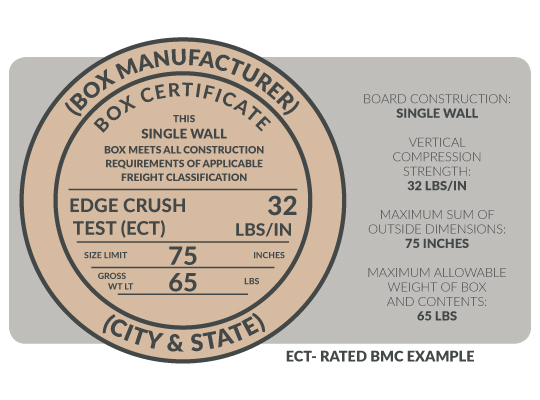
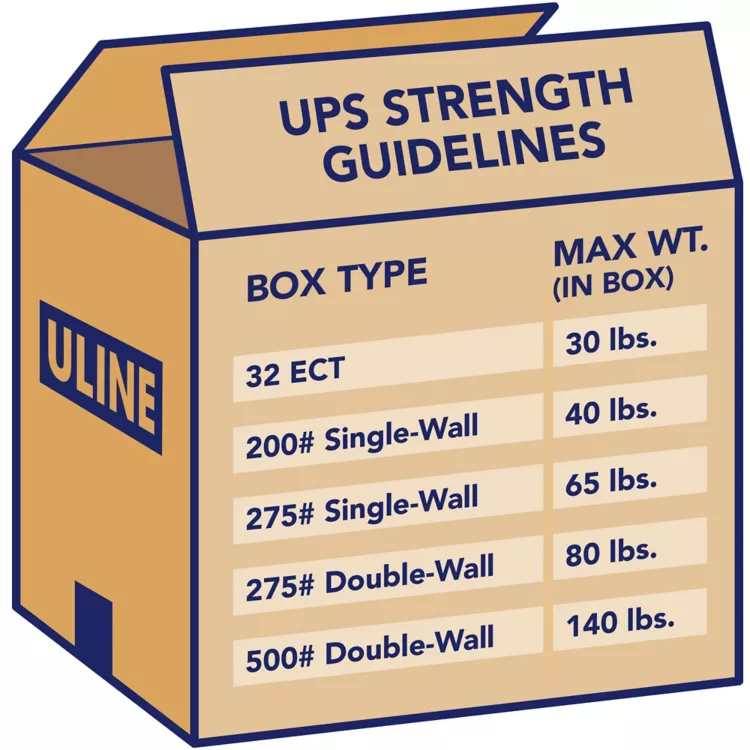
You can do all sorts of math to figure this out, but I think we've all purchased enough stuff from Amazon to know how that Amazon packaging is in inadequate. Amazon is focused on cost effectiveness since a huge number of customers use Prime Free Shipping. Weight of cardboard is one way to decrease your carbon footprint and decrease your shipping costs. There are even geographic differences. When you're dealing with the volumes that you do with Amazon, they can accept a certain amount of shipping damage for the cost savings of using less packaging.
In terms of your carbon footprint, nothing is worse than selling a piece of audio gear only to have it be damaged and requiring shipping to a repair depot, or worse, being thrown to the landfill. Just as you learned about storage tape vs. shipping tape, there are storage boxes vs. shipping boxes. As long as you get shipping boxes, you'll be OK using common sense.
I actually prefer to buy shipping boxes from FedEx due to convenience, regardless of the shipping service I'm using. Their 20x20x12 standard box and 24x24x18 heavy duty box fits a lot of typical audio components. Heavy duty moving boxes from Home Depot are good choices as well if you want different sizes.
Step 3: Taping Up Your Boxes
If you have a robust box and robust tape, you should just need to use the H-pattern. Use a single piece of tape to span the entirety of the longest axis, overlaping at least 2-3 inches. Then apply tape to the short-axes on top of the first piece of tape, to generate the H pattern. Although FedEx shows overlap of tape on the corners, I find that this increases the likelihood of the tape peeling off. When you second-guess the strength of your box, you can use a Tic-tac-toe pattern or a snowflake pattern, however when you do this, you'll quickly see that more tape increases the likelihood of one piece of tape lifting off and pulling the rest with it.
More tape isn't better -- more tape means more opportunities for automated sorting stuff to get caught on something and then have an additional point of failure.
Remember how I said we wanted hot melt adhesive tape for the strength? These have three layers, the adhesive, the actual film that provides strength, and then a "release" layer which makes it easy for the adhesive to come off the surface-side of the tape so that it peels off easily. This release layer makes it easy to avoid tearing the tape as you remove it from the spool and easy to work with, but it means that the second layer of tape ON TOP of the first layer of tape will have minimal grabbing power because there is an intentional release layer. So everytime you cross tape, that's an opportunity for the tape to lift off and act as something that gets caught during automated processing.
Step 4: Rigid Foam, Bubble Wrap, and Loose Peanuts/Craft Paper
If you don't have the product-specific highly contoured foam, you'll likely need to use a protective barrier of some sort.
I don't recommend loose peanuts. They get into the nooks and crannies of the audio gear and provide minimal actual protection unless it's being used as a layer between an inner and outer box. Bubble wrap is a good and effective strategy for many products.
However, you'll find that heavy amplifiers will pop bubble wrap just under their own weight. In this case, using rigid structural foam is a good idea. Extruded polystrene rigid insulation boards are one of the best ways to reinforce the base of a box. You can find them from places like Home Depot. Again, while this seems like it's a waste of money and you're adding more to landfills, it's a lot worse to destroy expensive working audio equipment. These come in a convenient 24x24" size (perfect for that 24x24x18 FedEx box I mentioned) and are relatively lightweight for the amount of structural support they offer. You can also cut them to size using a box-cutter by scoring the foam with the blade and then bending the foam to break it along the line that you have cut.
You can see how I can use a foam board to provide structural support to the box.
Your goal is to prevent the item from being crushed from outside the box, and just as importantly to prevent items from moving inside the box. You need to protect fragile elements like bindings posts and switches. You have to protect these by sealing them in thick bubble wrap or open cell foam, or even building some sort of block.
Example: Sonic Frontiers SFS-80 with fragile switches and binding posts.
I took an inner box that was just a bit too small and cut an opening to allow these to protrude out. I then took a block of foam that would provide a clear gap between the outer box and inner box which acts as a stop. I can then fill the area with added packing material.
In the inner box, I used the foam board along the sides and rear and then put a top layer. The inner box therefore is protected on 5 sides. I provided the sixth protective barrier (front of the unit) in the gap between the outer and inner box.
According to TMR Audio, 90% of the damage they see is from the corners. So pay extra attention to the corners!
A few other key points
- Your item cannot shake or wobble inside of the box. Double boxes or adding extra room for padding is dangerous if it just allows your item to jostle around. Think of the seat belt analogy versus your car's chassis/bumpers. The extra boxes are the bumpers, but you need seatbelts even in a car with great crumple zones and bumpers.
- Once you are ready to tape everything up, try jostling and rolling the box around and seeing how the object moves in all six axes first. In general, for something heavy, it'll get transferred in such a way that the labels remain face up, but you want the box and contents to move as a single unit. Slightly overstuffing the bubble wrap can help minimize the movement of items inside the boxes.
- You can use Blue Painter's tape to secure things as they will not leave a residue on products within normal shipping times. Be careful around labels/decals when using tape since the release might not be perfect.
- Ask yourself if that box would survive a 2-3 foot fall. That's a good metric for protection.
Step 5: Communicate
You cannot do much to make the automated sorted go smoothly other than avoiding too much tape on a shipping label. FedEx suggests putting the label on the top surface to maximize the chances that the "keep upright" is maintained, but from these YouTube videos, it seems like the automated sorting checks multiple sides for a label and it isn't guaranteed to remain in its ideal position and the UPS video actually shows workers flipping the boxes upside down.
One of the most important parts of shipping is to communicate when you're shipping something that is deceptively heavy for the size of the box. When you're shipping heavy items, it's helpful to let people know. UPS has official labels that they want you to add, but you can also print out whatever you want. You can even let them know if a product has uneven weight distribution. This helps the driver take better care of your packages. A fragile sticker doesn't help much since no one is intentionally being rough with the package. Sometimes, I will put on a label "Do Not Throw: Contains Fragile Scientific Instrument."
When I had my Linn LP12 shipped, I used reverse psychology. Usually audio gear is heavier than you think for the size of the box. With the turntable, I asked the shipper to use a giant extra-large moving box from Home Depot, using as much bubble wrap as needed to put the LP12 in the center, using blue tape to secure the tonearm and any moving parts. For the size of the box, one would expect something heavy and instead it was very light. For something fragile, having something "look" heavy by using an oversized box can help the team be a bit more careful.
I've had drivers ask me to help them bring heavy packages in (110 lb subwoofer). By policy they are SUPPOSED to use a hand truck and do it themselves, but some commercial shippers print shipping labels that state the package weight as 0 lbs (so that it's billed later at exactly the right amount) which can make it tough for some drivers. When I ship stuff out that's heavy, I print out a "two person lift" label -- even though we all know that the delivery drivers typically work on their own. This at least prepares the driver for the package's weight and if there are multiple trucks that service your area, maybe the stronger driver is the one that takes the heavier package.
Step 6: Choose your level of service
For audio gear, I've always just gone with Ground shipping. It gets pretty expensive to try to ship things by air. That said, for something extremely high value, some companies recommend going with 2-day air shipping to minimize excessive handling. Outside the world of premium audio are premium telescopes. Takahashi telescopes are hand-crafted telescopes that often require months to years of wait. In order to maintain your warranty, these telescopes must always be shipped via 2nd Day Air or faster in order for the full warranty to be in force. (You can see how they make them by hand; use Auto-Generated-Auto-Translated Closed Captions). Takahashi had this requirement in the pre-pandemic, pre-Amazon world and with the volume of today's packages, I can only imagine it's worse!
While we often think of flagship camera lenses as being super sharp, they are still massed produced. Something like a Canon 400mm f/2.8 has a Strehl ratio of 0.8 at best. The Strehl Ratio means that if you had a single point of light (i.e. a star, because it's so far away) all of the light can be focused to a single point at the focal plane. A theoretically perfect lens has a Strehl ratio of 1.0 and flagship telescopes from companies like Takahashi and Astro-Physics achieve Strehl Ratio's of 0.99 or better. This is done by individually correcting lenses and collimating them, and in the case of Astro-Physics, they even measure the refractive index of individual glass melts used in each lot and make subtle modifications to the optical formula based upon that batch. There is machine polishing (smoothness of the surface) but optical figuring (how close the curve matches the intended design) is surprisingly best done by hand. I don't think anything in audio has that level of extreme rarity/production value, but it's good to know that premium telescopes which range anywhere from $1,000 to $20,000 are almost always shipped 2nd Day Air.
Good luck, and don't blame me if your package falls off the conveyor belt and your gear is damaged...
Have other opinions or advice? Feel free to add to this thread.
I have been happy with USPS, UPS, and FedEx and have had my horror stories from all three. There can be a lot of variability with the delivery person assigned to your home, the use of temporary workers during the Holiday season, and simply bad luck. The thing to remember is that there are HUGE amounts of boxes going through the system and that translates into a lot of automated sorting. I don't work for any of the shipping companies, and I don't do commercial shipping, so if I have made a mistake, please let me know. I think I've done a lot of home-brew shipping of stuff without factory packaging.
My claim to fame is buying a Linn LP12 with no original packaging, no dust cover, or stylus cover featuring an irreplaceable Monster Cable Sigma 2000 moving coil cartridge from an estate sale where the selling party had minimal knowledge of audio gear but a willingness to take the packaging steps necessary to ensure its safe arrival (since I offered to pay a "handling fee" to go with the shipping). The most impressive packaging job I've seen was buying a JBL S/2600 "Baby Everest" from Japan. These are 125lb floor standing speakers. This was dedicated freight where a box truck was needed to deliver the speakers. When the driver opened the rear gate, he was mortified to see that the strap holding the speaker upright to the side of the vehicle had failed and the speaker had fallen off the wood pallet and keeled over to its side at some point during transit -- and there was zero damage.
Q. I have an original, never before released, master copy of a Beatles recording they made. There is one in the world, it's priceless, and I need to ship it with maximum insurance.
A. You want USPS registered mail
Once of the surprising things about shipping insurance is that declared value is different from insured value, and just because you insure something for a certain amount, the shipping company can still blame you for shoddy packaging, especially if it's not the manufacturer's packaging. In this scenario though, it's worth remembering the United States Postal Service has Registered Mail. This is an add-on to regular First-Class Mail (documents), USPS Ground Advantage (low cost mail) and Priority Mail.
With Registered Mail, you are paying extra for a full chain of custody from the moment you hand your package to the Post Office. Every time the package goes from one individual to the next or one office to the next, there will be a signature trail that is manually done. When the item is not in transit, it is stored in a specifically locked safe, room or cage with separate access requirements that the regular mail. Things can be insured for the true cost/market value of the product up to $50,000.
It sounds amazing, but it's not perfect. The USPS Office of the Inspector General did random inspections and found a lot of post offices were not following all of the rules. Still, the fact that you have random audits brings things up to a level of care that you don't get with other services, and if they really do lose your package, they will cover the insurance. The biggest consequence to Registered Mail is that it involves human processing along the entire way, so it is much slower because the priority is knowing where the package is and who the package is with at any given time.
When shipping items through UPS or FedEx, you need to provide proof of value and they can always complain that you didn't properly package the items. While insurance can cover lost, damaged goods can be harder to get insurance pay out UNLESS you had FedEx Office or the UPS Store or Customer Service Center package the item. Sometimes, the local store isn't that great at packaging since they tend to use craft paper. One option is to box the item yourself and then pay to have it double boxed with the insurance. Since the FedEx or UPS center is packaging the item, you have a better chance of getting covered.
With Registered Mail, you are paying extra for a full chain of custody from the moment you hand your package to the Post Office. Every time the package goes from one individual to the next or one office to the next, there will be a signature trail that is manually done. When the item is not in transit, it is stored in a specifically locked safe, room or cage with separate access requirements that the regular mail. Things can be insured for the true cost/market value of the product up to $50,000.
It sounds amazing, but it's not perfect. The USPS Office of the Inspector General did random inspections and found a lot of post offices were not following all of the rules. Still, the fact that you have random audits brings things up to a level of care that you don't get with other services, and if they really do lose your package, they will cover the insurance. The biggest consequence to Registered Mail is that it involves human processing along the entire way, so it is much slower because the priority is knowing where the package is and who the package is with at any given time.
When shipping items through UPS or FedEx, you need to provide proof of value and they can always complain that you didn't properly package the items. While insurance can cover lost, damaged goods can be harder to get insurance pay out UNLESS you had FedEx Office or the UPS Store or Customer Service Center package the item. Sometimes, the local store isn't that great at packaging since they tend to use craft paper. One option is to box the item yourself and then pay to have it double boxed with the insurance. Since the FedEx or UPS center is packaging the item, you have a better chance of getting covered.
FedEx puts out a nice document on best practices with a lot of nice detail and photos. UPS has a guide also, but has fewer photos.
Step 1: Know your tape adhesive
If you have had to move a large apartment or home, you've likely had to deal with a lot of moving boxes. While it can be tempting to get the cheapest tape you can find off Amazon, you'll often find that generic ones falls apart or they'll have a noxious odor. Choosing the right tape is actually essential when shipping heavy audio gear. The best packaging doesn't help if your tape fails you. For convenience, I will refer to 3M consumer tapes since they're readily available and my preferred choice. There's a whole world of industrial tapes too.
You basically have two options for adhesives: Acrylic and Hot Melt Adhesives.
Acrylic adhesives are often used in "storage tape"
These types of adhesives are an emulsion which allows to deal with dusty boxes and are also UV resistant and water-resistant. So, it's theoretically a good choice if you're shipping during rainy season or sending stuff somewhere humid. But you know what acrylic tape is bad for? Strength.
Hot melt adhesives are probably what you want when shipping electronics. These use a synthetic rubber/resin adhesive which isn't as UV resistant, temperature or water resistant as the acrylic emulsion adhesive but they are stickier and won't accidentally release. Hot melt adhesives are what you want for rough handling of boxes, such as with automated processes.
What's the difference between the various hot melt adhesive products from Scotch? No real idea, but there are subtle differences in the advertised performance.
Thickness
Tensile Strength (Longitudinal)
Rated Temperature
Rated weight
Adhesion to Stainless Steel Test Panel
Elongation before break
Scotch General Purpose | 2.2 mil |
Scotch Storage | 2.4 mil |
Scotch Sure Start | 2.6 mil |
Scotch Box Lock, Heavy Duty, Tough Grip | 3.1 mil |
Tensile Strength (Longitudinal)
Scotch Storage | 40 pounds per inch |
Scotch Sure Start | 42 pounds per inch |
Scotch Box Lock, Heavy Duty, Tough Grip | 46-47 pounds per inch |
Rated Temperature
Scotch Heavy Duty | 40F to 120F |
Scotch Box Lock | -15F to 140F |
Rated weight
Scotch Tough Grip, Heavy Duty | 80 lbs |
Scotch 311+ (industrial acrylic adhesive; 2.05 mil thickness) | < 20 lbs |
Scotch 371+ (industrial hot melt adhesive; 2.1 mil thickness) | < 20 lbs |
Scotch 373+ (industrial hot melt adhesive; 2.5 mil thickness) | 80 lbs |
Scotch 375+ (industrial hot melt adhesive; 3.1 mil thickness) | 100 lbs |
Adhesion to Stainless Steel Test Panel
Scotch 371+ | 45 ounces per inch |
Scotch 373+ | 50 ounces per inch |
Scotch 375+ | 61 ounces per inch |
Scotch Box Lock | 65 ounces per inch |
Elongation before break
Scotch 371+ | 160% |
Scotch 373+ | 160% |
Scotch 375+ | 119% |
Scotch Box Lock | 150% |
TLDR? Heavy Duty is probably better for heavier objects because it has the official 80 lb rating but is only rated to as low as 40 degrees F. The Box Lock has really high adhesion, even against the industrial tapes, but breaks at 150% elongation as compared to 160% suggesting that it might not hold heavier objects. The Box Lock has a wider range of operating temperatures including sub-freezing temperatures.
Step 2: Know your boxes
There are companies that are known for shipping fragile items safely. McIntosh is one. If you're dealing with well-established brands with good perceived customer service, step 1 is to reach out to the company for boxes. Without naming names, I've gotten huge speaker boxes and packaging material for free from an audiophile speaker company just for asking and purchased dedicated boxes with the product specific foam inserts from other companies at very reasonable prices. If you're dealing with something expensive and fragile, reach out to the company to see if you can buy a replacement shipping box first. In most cases, the shipping box and product box are the same -- but that is not always true.
People know about single- and double- wall board, but even for double walled cardboard, there are different types of corrugation/flutes and even different standards for box ratings.
You can do all sorts of math to figure this out, but I think we've all purchased enough stuff from Amazon to know how that Amazon packaging is in inadequate. Amazon is focused on cost effectiveness since a huge number of customers use Prime Free Shipping. Weight of cardboard is one way to decrease your carbon footprint and decrease your shipping costs. There are even geographic differences. When you're dealing with the volumes that you do with Amazon, they can accept a certain amount of shipping damage for the cost savings of using less packaging.
In terms of your carbon footprint, nothing is worse than selling a piece of audio gear only to have it be damaged and requiring shipping to a repair depot, or worse, being thrown to the landfill. Just as you learned about storage tape vs. shipping tape, there are storage boxes vs. shipping boxes. As long as you get shipping boxes, you'll be OK using common sense.
I actually prefer to buy shipping boxes from FedEx due to convenience, regardless of the shipping service I'm using. Their 20x20x12 standard box and 24x24x18 heavy duty box fits a lot of typical audio components. Heavy duty moving boxes from Home Depot are good choices as well if you want different sizes.
Step 3: Taping Up Your Boxes
If you have a robust box and robust tape, you should just need to use the H-pattern. Use a single piece of tape to span the entirety of the longest axis, overlaping at least 2-3 inches. Then apply tape to the short-axes on top of the first piece of tape, to generate the H pattern. Although FedEx shows overlap of tape on the corners, I find that this increases the likelihood of the tape peeling off. When you second-guess the strength of your box, you can use a Tic-tac-toe pattern or a snowflake pattern, however when you do this, you'll quickly see that more tape increases the likelihood of one piece of tape lifting off and pulling the rest with it.
More tape isn't better -- more tape means more opportunities for automated sorting stuff to get caught on something and then have an additional point of failure.
Remember how I said we wanted hot melt adhesive tape for the strength? These have three layers, the adhesive, the actual film that provides strength, and then a "release" layer which makes it easy for the adhesive to come off the surface-side of the tape so that it peels off easily. This release layer makes it easy to avoid tearing the tape as you remove it from the spool and easy to work with, but it means that the second layer of tape ON TOP of the first layer of tape will have minimal grabbing power because there is an intentional release layer. So everytime you cross tape, that's an opportunity for the tape to lift off and act as something that gets caught during automated processing.
Step 4: Rigid Foam, Bubble Wrap, and Loose Peanuts/Craft Paper
If you don't have the product-specific highly contoured foam, you'll likely need to use a protective barrier of some sort.
I don't recommend loose peanuts. They get into the nooks and crannies of the audio gear and provide minimal actual protection unless it's being used as a layer between an inner and outer box. Bubble wrap is a good and effective strategy for many products.
However, you'll find that heavy amplifiers will pop bubble wrap just under their own weight. In this case, using rigid structural foam is a good idea. Extruded polystrene rigid insulation boards are one of the best ways to reinforce the base of a box. You can find them from places like Home Depot. Again, while this seems like it's a waste of money and you're adding more to landfills, it's a lot worse to destroy expensive working audio equipment. These come in a convenient 24x24" size (perfect for that 24x24x18 FedEx box I mentioned) and are relatively lightweight for the amount of structural support they offer. You can also cut them to size using a box-cutter by scoring the foam with the blade and then bending the foam to break it along the line that you have cut.
You can see how I can use a foam board to provide structural support to the box.
Your goal is to prevent the item from being crushed from outside the box, and just as importantly to prevent items from moving inside the box. You need to protect fragile elements like bindings posts and switches. You have to protect these by sealing them in thick bubble wrap or open cell foam, or even building some sort of block.
Example: Sonic Frontiers SFS-80 with fragile switches and binding posts.
I took an inner box that was just a bit too small and cut an opening to allow these to protrude out. I then took a block of foam that would provide a clear gap between the outer box and inner box which acts as a stop. I can then fill the area with added packing material.
In the inner box, I used the foam board along the sides and rear and then put a top layer. The inner box therefore is protected on 5 sides. I provided the sixth protective barrier (front of the unit) in the gap between the outer and inner box.
According to TMR Audio, 90% of the damage they see is from the corners. So pay extra attention to the corners!
A few other key points
- Your item cannot shake or wobble inside of the box. Double boxes or adding extra room for padding is dangerous if it just allows your item to jostle around. Think of the seat belt analogy versus your car's chassis/bumpers. The extra boxes are the bumpers, but you need seatbelts even in a car with great crumple zones and bumpers.
- Once you are ready to tape everything up, try jostling and rolling the box around and seeing how the object moves in all six axes first. In general, for something heavy, it'll get transferred in such a way that the labels remain face up, but you want the box and contents to move as a single unit. Slightly overstuffing the bubble wrap can help minimize the movement of items inside the boxes.
- You can use Blue Painter's tape to secure things as they will not leave a residue on products within normal shipping times. Be careful around labels/decals when using tape since the release might not be perfect.
- Ask yourself if that box would survive a 2-3 foot fall. That's a good metric for protection.
Step 5: Communicate
You cannot do much to make the automated sorted go smoothly other than avoiding too much tape on a shipping label. FedEx suggests putting the label on the top surface to maximize the chances that the "keep upright" is maintained, but from these YouTube videos, it seems like the automated sorting checks multiple sides for a label and it isn't guaranteed to remain in its ideal position and the UPS video actually shows workers flipping the boxes upside down.
One of the most important parts of shipping is to communicate when you're shipping something that is deceptively heavy for the size of the box. When you're shipping heavy items, it's helpful to let people know. UPS has official labels that they want you to add, but you can also print out whatever you want. You can even let them know if a product has uneven weight distribution. This helps the driver take better care of your packages. A fragile sticker doesn't help much since no one is intentionally being rough with the package. Sometimes, I will put on a label "Do Not Throw: Contains Fragile Scientific Instrument."
When I had my Linn LP12 shipped, I used reverse psychology. Usually audio gear is heavier than you think for the size of the box. With the turntable, I asked the shipper to use a giant extra-large moving box from Home Depot, using as much bubble wrap as needed to put the LP12 in the center, using blue tape to secure the tonearm and any moving parts. For the size of the box, one would expect something heavy and instead it was very light. For something fragile, having something "look" heavy by using an oversized box can help the team be a bit more careful.
I've had drivers ask me to help them bring heavy packages in (110 lb subwoofer). By policy they are SUPPOSED to use a hand truck and do it themselves, but some commercial shippers print shipping labels that state the package weight as 0 lbs (so that it's billed later at exactly the right amount) which can make it tough for some drivers. When I ship stuff out that's heavy, I print out a "two person lift" label -- even though we all know that the delivery drivers typically work on their own. This at least prepares the driver for the package's weight and if there are multiple trucks that service your area, maybe the stronger driver is the one that takes the heavier package.
Step 6: Choose your level of service
For audio gear, I've always just gone with Ground shipping. It gets pretty expensive to try to ship things by air. That said, for something extremely high value, some companies recommend going with 2-day air shipping to minimize excessive handling. Outside the world of premium audio are premium telescopes. Takahashi telescopes are hand-crafted telescopes that often require months to years of wait. In order to maintain your warranty, these telescopes must always be shipped via 2nd Day Air or faster in order for the full warranty to be in force. (You can see how they make them by hand; use Auto-Generated-Auto-Translated Closed Captions). Takahashi had this requirement in the pre-pandemic, pre-Amazon world and with the volume of today's packages, I can only imagine it's worse!
While we often think of flagship camera lenses as being super sharp, they are still massed produced. Something like a Canon 400mm f/2.8 has a Strehl ratio of 0.8 at best. The Strehl Ratio means that if you had a single point of light (i.e. a star, because it's so far away) all of the light can be focused to a single point at the focal plane. A theoretically perfect lens has a Strehl ratio of 1.0 and flagship telescopes from companies like Takahashi and Astro-Physics achieve Strehl Ratio's of 0.99 or better. This is done by individually correcting lenses and collimating them, and in the case of Astro-Physics, they even measure the refractive index of individual glass melts used in each lot and make subtle modifications to the optical formula based upon that batch. There is machine polishing (smoothness of the surface) but optical figuring (how close the curve matches the intended design) is surprisingly best done by hand. I don't think anything in audio has that level of extreme rarity/production value, but it's good to know that premium telescopes which range anywhere from $1,000 to $20,000 are almost always shipped 2nd Day Air.
Good luck, and don't blame me if your package falls off the conveyor belt and your gear is damaged...
Have other opinions or advice? Feel free to add to this thread.