- Joined
- May 1, 2021
- Messages
- 427
- Likes
- 1,309
I was recently asked what the effect of mounting drivers vertically (planar with the floor) versus traditional mounting with the driver axis pointing towards the listener. The former is for example the case for the BeoLab5:
In both cases gravity will inevitably act on the driver, and if a particular mounting is problematic, then it would be expected that others will be too (because of the shape of the driver and the torques involved), and it would seem empirically that no such issues have been reported.
Anyway, it is still good to do some modelling of this. I was asked if it would be easy enough to simulate with COMSOL, but for the case of a vertically mounted driver, it can actually be done much simpler.
The gravity will act on the distributed mass of the driver, and so one can look up the moving mass and do the calculations, first via Newton's second law:
F_mass=Mms*g
where g is 9.82 m/s^2. As this is countered by the stiffness of the driver setup (surround and spider), one can set the two equal with Hooke's law with the stiffness Kms=1/Cms:
Mms*g=Kms*x
such that
x=g*Mms/Kms
So, for a particular case that I simulated years back, I find that
x=9.82 m/s^2 * 8 g / (0.43 mm/N)^-1
which is equal to 0.033 mm.
This can also be simulated via a Finite Element Setup, and so I made a static study with gravity applied to the old case in question:
As can be seen, the displacement value found via this numerical setup gives a similar value of 0.03 mm static displacement.
This initial displacement that the entire frequency response now is a perturbation to is not likely to affect any conclusions, especially not when taking into account the manufacturing tolerances.
The actual displacement of course needs to be evaluate on a case-by-case basis, but nothing alarming is seen in this quick investigation.
---
Simulations are great, and I typically trust them (mine, at least) over measurements, and have often found via simulation that measurements had to be wrong. But any simulation should be accompanied by a simpler analytical model or description for sanity checks, and for the present case an analytical approach is much faster and just as a accurate as a full-blown simulation.
Merry X-Mas from Acculution!
René
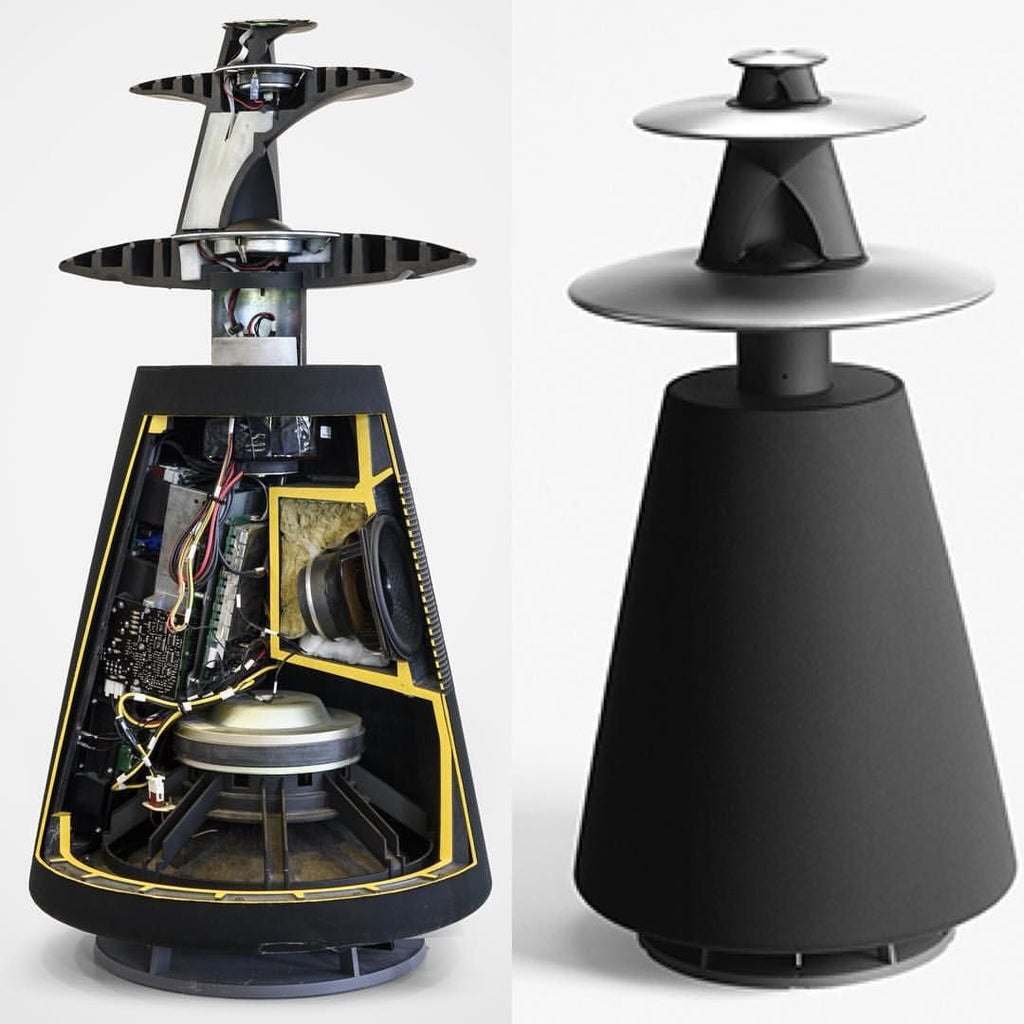
In both cases gravity will inevitably act on the driver, and if a particular mounting is problematic, then it would be expected that others will be too (because of the shape of the driver and the torques involved), and it would seem empirically that no such issues have been reported.
Anyway, it is still good to do some modelling of this. I was asked if it would be easy enough to simulate with COMSOL, but for the case of a vertically mounted driver, it can actually be done much simpler.
The gravity will act on the distributed mass of the driver, and so one can look up the moving mass and do the calculations, first via Newton's second law:
F_mass=Mms*g
where g is 9.82 m/s^2. As this is countered by the stiffness of the driver setup (surround and spider), one can set the two equal with Hooke's law with the stiffness Kms=1/Cms:
Mms*g=Kms*x
such that
x=g*Mms/Kms
So, for a particular case that I simulated years back, I find that
x=9.82 m/s^2 * 8 g / (0.43 mm/N)^-1
which is equal to 0.033 mm.
This can also be simulated via a Finite Element Setup, and so I made a static study with gravity applied to the old case in question:
As can be seen, the displacement value found via this numerical setup gives a similar value of 0.03 mm static displacement.
This initial displacement that the entire frequency response now is a perturbation to is not likely to affect any conclusions, especially not when taking into account the manufacturing tolerances.
The actual displacement of course needs to be evaluate on a case-by-case basis, but nothing alarming is seen in this quick investigation.
---
Simulations are great, and I typically trust them (mine, at least) over measurements, and have often found via simulation that measurements had to be wrong. But any simulation should be accompanied by a simpler analytical model or description for sanity checks, and for the present case an analytical approach is much faster and just as a accurate as a full-blown simulation.
Merry X-Mas from Acculution!
René