What do you do when it rains again for days on end ...
You might be thinking about the past, when everything was nice. And that's what I do now too:
Speaker stand with SCHUBIDU. SCHUBIDU was born in Berlin - a permanent loan from my daughter.
The pipe only looks thinner because of the flash at the top.
My self-made, very simple speaker stand:
Built in one afternoon (2004) with parts I had in my garage. And because of the thread topic I show you the details for DIY:
Neumann KH310 (since 2016):
Place the cork board underneath so that the KH310 rests absolutely firmly on the upper wooden board.
All feet of the speaker stand must have firm contact with the floor. Feel it with your index finger when you try to wiggle the stand.
Check this after a few weeks.
Parts of the speaker stand:
P1: Upper wooden disc (glued wood panel beech 28 x 250 mm)
P2: Lower wooden disc (glued wood panel beech 28 x 460 mm)
P3: Small washers with spring washers (P6) and nuts
P4: Large washers at the ends of the pipe (P10)
P5: Rubbers in the pipe (P10) for centring and fastening the threaded rod (P9) with nuts
P6: 2 to 3 spring washers on each side
P7: Velcro tape
P8: Adjustable feet (the thread is cut into the wooden disc (P2))
P9: Threaded rod D 12 mm
P10: Pipe (stainless steel D 48 x 2 mm)
For P1/P2:
Are created with the wood router in several steps. The parallel guide of the wood router was extended with two threaded rods.
Use a drill stand that stands on the glued wood panels so that the holes are drilled at an angle of 90°.
I had the least waste with the dimensions mentioned above.
If the gluing is of poor quality, individual wood segments can break out.
For P3:
Use a router to mill the blind hole at the top so that (P3) does not protrude.
For P4:
The pipe are fastened between these washers with (P3).
Centring during assembly: only by hand / with adhesive tape / with a suitable washer
For P5:
Were spare parts for an old Mercedes car of mine. First attach the lower rubber with the nuts, fill the pipe with fine dry sand and then attach the upper rubber. The two inner nuts (left and right of (P9)) must of course be secured with one nut each.
For P8:
The length of the feet determines whether you can still work under the glued beech panel with a hoover.
I could also remove dust again ...
Should be painted black - been on my to-do list intermittently since 2004 ...
Alternatives for hard floors: e.g. Allen screws: Allen to the floor and with a saw slot for screwdrivers, ...
For P10:
Precise 90° cut if you don't have a machine for this (like me): e.g. wrap a sheet of photocopy paper around the pipe at the desired position so that all layers of paper are on top of each other. Cut the pipe with a diamond disc at a distance of at least approx. 0.5 mm from the paper. The easiest way is for a helper to turn the pipe slowly on a slightly open vice.
Neumann KH310 - Resonances of the grille:
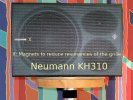
The resonances of the metal grilles can be measured and heard when the grille is struck with an object. The resonances are audibly and measurably reduced with a few magnets in the area of the bass loudspeaker. The magnet must not be too thick so that the bass speaker does not strike.
Additional magnets on the other side would reduce the resonances even further, but this would lead to reflections (which have not yet been measured).
SCHUBIDU is happy that it is not raining.
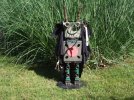