Looneybomber
Active Member
- Joined
- Sep 23, 2022
- Messages
- 124
- Likes
- 134
I saw that video a few days ago. I was shocked at some of the gaps between the braces and the cabinets. Sloppy!
3:40, The person hammering down the one brace didn’t hammer it down all the way. The curved portion doesn’t touch the enclosure.
4:25, The top/bottom plate fitting inside the enclosure has huge gaps.
7:15, The braces on the side of the enclosure, parallel with the baffle, which they glue the baffle to are not flush with the perpendicular ones. How do they even get a good bond if they can’t get the boards pressed tight against the baffle?
Those are the gaps I’d expect to see in a DIY thread from a person with minimal tools and experience. Not a $14k speaker.
www.audiothesis.com
3:40, The person hammering down the one brace didn’t hammer it down all the way. The curved portion doesn’t touch the enclosure.
4:25, The top/bottom plate fitting inside the enclosure has huge gaps.
7:15, The braces on the side of the enclosure, parallel with the baffle, which they glue the baffle to are not flush with the perpendicular ones. How do they even get a good bond if they can’t get the boards pressed tight against the baffle?
Those are the gaps I’d expect to see in a DIY thread from a person with minimal tools and experience. Not a $14k speaker.
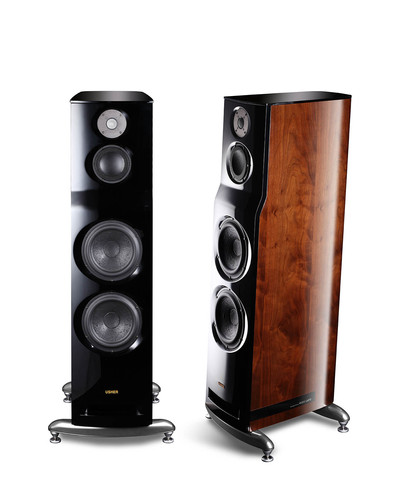
Usher Audio ML-802 | AudioThesis
Magnesium Aluminum drivers paired with two 8955A bass woofers and is offered in two finishes: Walnut and Macassar. The base model is offered in a satin finish while an upgrade to a high gloss piano is available. Specifications: 3-way system : 1.25" MA tweeter, 5" MA midrange, 8" woofer...
